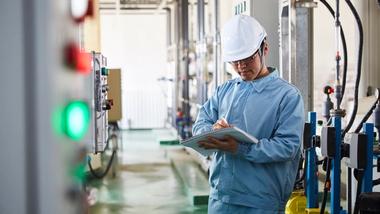
Providing skills for life
Average read time: 10 minutes
Ongoing learning is at the heart of our culture – and our commitment to helping people stay fit for the future of work.
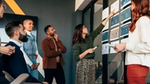
There’s no such thing as a job for life in today’s world. Automation continues to advance in manufacturing, and people in all industries are having to learn new skills as technologies, the economy and jobs evolve. It’s a theme that was echoed at our first Future of Work Summit, where participants highlighted the irreversible momentum driving change in working practices and the impact of the Fourth Industrial Revolution.
But the future of work is much more than just the relationship between technology and humans. It’s about completely new ways of working, the need for belonging, and about creating value – for the individual as well as the organisation.
So it’s more important than ever to have a plan for the future and the skills to match. We’re committed to helping our people equip themselves to pursue their idea of meaningful work in an ever-changing world, a goal we’ve set as part of our Unilever Compass.
50% Of the global workforce will need to reskill by 2025 (World Economic Forum)
The idea of continuing to learn to stay fit for the future is at the heart of Unilever. The core belief underpinning our approach is that people with purpose thrive. And to ensure they do thrive, we have a duty to help our people adapt to the impact of evolving technologies and ways of working. But this isn’t something we’re doing to people – we’re doing it with them by working closely with individuals and with employee and union representatives to find solutions that work for everyone, not just for our business.
Reskilling for the future
We’re aiming to reskill or upskill our employees with future-fit skills. We’re doing this by supporting them to proactively develop an individual Future-Fit Plan. The Future-fit Plan is a development framework that supports employees in building skills in line with their purpose, wellbeing and leadership behaviours.
They start by clarifying their purpose – the things that are most meaningful to their lives and work. Based on data from 3,500 employees across 14 countries, we now have statistical evidence of the link between purpose and motivation through independent research led by the London School of Economics in the UK. This found that people who had taken part in our purpose workshops reported an impressive 49% jump in intrinsic motivation compared to those who hadn’t, while a quarter said they were more inspired to go the extra mile in their job.
The Future-fit Plan plays a crucial role in connecting employees to the priority skills Unilever needs for current roles and future work. Employees use their plan to guide their career path and identify and develop the skills they’ll need to succeed. This might involve enhancing their skills for their current role (upskilling), training to move to a different role in Unilever (reskilling), or preparing for careers and opportunities beyond our business. 30% of our office-based employees now have an active Future-fit Plan in place.
To support their development, employees are guided to personalised learning materials and can engage with others on a similar learning track via Degreed, our online learning hub, which our employees accessed over 2.4 million times in 2022. And through our Flex Experiences programme, people gain hands-on experience by working on assignments with other teams around Unilever.
We continue to expand the range and reach of our training and development programmes, along with access to a range of development resources. Even with the volatile economic context that has seen other companies pull back on their learning investment, in 2022 we spent around €77 million on training and development and estimated average of €644 per employee. From the data we can collect through our learning platforms and other training offered to our employees (those who have access to our IT systems, not including temporary and seasonal workers), we estimate that employees received on average 27 hours of training and development in 2022.
Furthermore, we continue to focus on equipping our people with future-fit skills. These include skills we’ve prioritised as important enablers of business growth, such as data science, agile working, and digital expertise for manufacturing. In 2022 we upskilled or reskilled 15% of our employees with these specific skills.
Ultimately, our Future-fit Plan approach ensures our people know the skills they need to be future-fit and how we can support them to develop these skills.
140 Certified Agile coaches at the end of 2022
Agile
We’re investing in creating an agile mindset amongst our people - it is fundamental to how we work. Our Agile programme is supporting our Compass Organisation to be just that.
In 2022, we continued building this capability for the business by appointing Agile coaches and training Scrum Masters (who are responsible for driving the process), for each of our Business Groups. These Agile Coaches and Scrum Masters underwent accredited development programme and are now upskilling our leaders, and teams, helping them embed Agile behaviours, skills and delivery processes. This is already resulting in business benefits through simplification and growth. By the end of 2022, we had 140 Agile coaches trained and certified, more than 100 trained Scrum Masters who have helped to connect over 2,200 employees to complete at least some form of Agile training.
Flex Experiences
Our in-house flexible working programme matches people with project opportunities in other business areas and locations to experience different roles and projects and build skills, without having to change their core role. The AI-powered talent marketplace allows our team leaders to resource projects at speed and helps employees develop their skills and build experience in line with their Future-fit Plan. In 2021 for example, Flex allowed us to reprioritise more than 57,000 hours to nearly 200 critical projects.
Responsible transformation
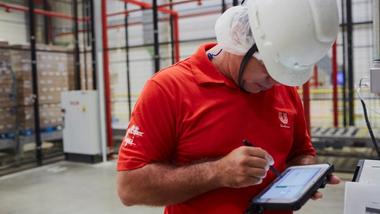
Automation is a key part of the fourth industrial revolution – where many jobs are changing or disappearing due to things like technology, new employment models and shifting workforce demographics.
97m The anticipated number of jobs created by automation (World Economic Forum)
According to the World Economic Forum, the integration of automation into working practices is expected to create 97 million jobs at the same time as replacing some 85 million jobs. And by 2025, the time spent on current work tasks by humans and machines is expected to be equal.
This is, of course, changing how we work – in some areas faster than others, like manufacturing. We’re looking at how technology can bring us together and allow us to use the power of human connection to achieve flexibility, inclusivity, purpose and sustainability. We’re analysing how our business will change and through our digital factory programme, we’re rolling out technology to enable our frontline workers to learn on the job and work more effectively.
Skills for the future of manufacturing
As manufacturing becomes more automated, the skills required by production teams will need to change from routine, highly regular activities to more autonomous roles that focus on problem solving and improvement. Our TaiCang factory in China is a good example of the factory of the future – it’s been recognised by the World Economic Forum (WEF) as the world’s most advanced ice cream factory for its use of Fourth Industrial Revolution (4IR) technologies. Three more of our factories are part of WEF’s Global Lighthouse Network: our personal care product factories in Hefei, China and Dubai in the UAE, as well as our Dapada home care products factory, which is the first FMCG factory in India to reach this status.
We’ve identified 65 new skills of the future for manufacturing and 45 for engineering. These range from asset management, data visualisation and data-driven decision making to robotic maintenance and the internet of things.
To support this shift, we’re using a number of different approaches to equip our teams with the training, technology and tools to allow them to work in a digital environment.
Going digital
Our Digital Factory Programme builds employees’ expertise in data acquisition and analytics, skills that are essential in operating our increasingly sophisticated factories.
Another of our initiatives, our Robotics and Automation Learning Programme, helps teams identify opportunities for using robotics and automation in their factory, warehouse or distribution centre.
And we’re using gamification to engage engineering teams in boosting their technical skills and to create personal learning plans.
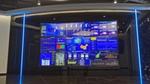
Training the trainers
We’re making use of new styles of training, such as the ‘train the trainer’ approach.
Our Casale factory in Italy has introduced this: training is carried out by the operators themselves, who have already received training and then share their knowledge with their colleagues.
As they live and breathe factory processes, employees are able to offer instant support in understanding questions and suggestions, which is proving particularly useful in building knowledge of new digital apps and digital factory operating systems.
We’re finding that collaboration also improves through this approach.
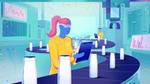
Using AI to identify people’s skills
We’re also testing digital technology to help us understand the skills our employees already have as well as the ones they’ll need for the future. Reskilling and upskilling are often seen as a time-consuming and costly exercise by businesses, so we’re looking to see if data and AI can help.
We’re essentially replacing job titles with skills - that means a complete reinvention of the way we do HR to develop a future-fit workforce.
Paddy Hull, our Vice President, Future of Work
In a research project with Walmart, Accenture and Skyhive (a workplace analytics start-up), we set out to uncover how to identify and unlock hidden skills and to thereby create innovative pathways for people to move between roles or organisations.
Unilever and Walmart identified several roles in 11 representative cities in the US, Europe and Latin America. Using AI, each role was broken into a collection of clearly defined skills such as experience with specific technologies or attention to detail. The pilot found that technology is better at identifying skills than people are. When people self-report on their skills, they identify on average 11 skills for a particular role; using technology, that number jumps to 34 skills.
Once roles are seen as a collection of skills, we can map the potential for cross-functional moves supported by focused learning and work experiences. On average, the pilot showed that people could be reskilled for new roles in completely different functions in just six months. Above all, it opened our eyes to the different opportunities we could offer our people in line with their passions and strengths – opportunities they may have considered out of reach previously. This supports our wider approach to reskilling, which recognises that providing learning on its own is not sufficient; people need on-the-job experience to build and demonstrate the skills they’re learning.
New technology, new skills
One of the tools we’ve developed as we roll out our Digital Factory Programme is BuildApp. It’s an app based on a factory manufacturing console which we’re using to digitise and optimise all our standard processes and increase productivity.
With real-time visibility on factory performance, BuildApp has 28 different modules that factory teams use to manage their operations. Employees use it to collect and share data, develop their own skills, stay connected through local and global communications, and access digital services such as self-service HR.
Live in around 100 factories around the world, this technology is leading to faster and more collaborative problem-solving that’s benefiting our business. For example, at our Leioa factory in Spain, we’ve used BuildApp to drive significant improvements such as an 11% reduction in waste and a 3.5% increase in productivity.
This technology will eventually create a frontline digital workplace across our manufacturing sites and also connect our factories more seamlessly with customers and suppliers.
Thinking differently transforms a factory’s future
We have a duty to help our people – including those in our supply chain – to adapt to the changing world of work. So through our Future Fit planning, we’re also helping them identify future employment opportunities and develop their skills and capabilities. Not only is this important for employees, but also for the communities in which our people live and work. Our Italian factory reimagined its future – and is now being transformed into a new recycling facility.