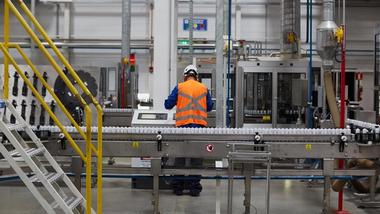
Our eco-efficiency reporting
Average read time: 6 minutes
Improving the eco-efficiency of our manufacturing sites and offices helps us cut their environmental impact, reduce running costs and enhance overall site performance.
Driving environmental improvements
Unilever has an extensive network of factories, offices, research laboratories and distribution warehouses. We aim to reduce the environmental footprint of our operations even as our business grows.
Our environmental management system provides a framework for continual improvement in our operational footprint. It helped us work towards the ambitious greenhouse gas, waste and water targets that were part of the Unilever Sustainable Living Plan and now the Unilever Compass which includes commitments on zero carbon operations and maintaining zero non-hazardous waste to landfill.
We’re working to achieve a 100% reduction in our operational Scope 1 and 2 GHG emissions from our factories, offices, research laboratories and warehouses by 2030, against a 2015 baseline. In 2022, we had reduced this by 68%.
In 2022, 93% of our electricity, and a third of our thermal energy came from renewable sources1. Our factories also achieved a full year of production without direct coal use, and we continue looking for ways to improve energy efficiency. In 2022, our factories reduced their operational energy consumption by 4%, versus 2021.
We’ve also been investing. In 2022, we invested €37 million in capital expenditure projects via our Clean Technology Fund resulting in an estimated 88,000 tonne reduction in GHG emissions – which mainly focused on renewable energy and resource efficiency. To inform our investment decision-making, we use an internal carbon price of €70 per tonne of CO2.
We set annual global targets for each of our eco-efficiency performance indicators to drive progress. These are supported by site-specific targets set by our regions and Business Groups. Each site is different, so the best ways to drive efficiency depends on use, scale, location and capacity.
Our Unilever Manufacturing System seeks to integrate sustainability through continual improvement, and investment in efficient equipment and new technologies. This includes regular audits of environmental performance by internal experts (see below for further details). Eco-efficiency is not just about reducing our environmental footprint. It makes good business sense. We collect information on costs, such as energy and water use from all manufacturing sites, through our environmental performance reporting system. This enables us to measure the financial benefits of our eco-efficiency programme.
For years we’ve invested in eco-efficiency projects across our factories, reducing CO2 from energy per tonne of production by 79% compared to 2008 and by 11% versus 2021. Recent investments include improving energy efficiency of lighting and manufacturing equipment, and installing heat recovery systems. We've committed to align our future capital expenditure with the Paris Agreement. As a first step, in 2021 we developed a bespoke digital tool to capture the GHG, water and waste impact data of all capital expenditure projects.
Our environmental management system
We developed the Unilever SHE Framework Standards in the 1990s and have kept improving and adapting them to our changing needs ever since. Currently, there are three SHE Framework Standards: Occupational Health & Safety, Environmental Care and Consumer Safety. Taken together, they describe a complete SHE Management System and apply to all organisations2 within Unilever.
Our environmental policy (Opens in a pop-up window ) outlines our individual and shared responsibilities to the environment. It is implemented through the commitments within the Unilever Compass.
SHE specific standards
Each organisation must identify and evaluate its products, operations, activities or services to determine those which have (or could have) a significant impact on the environment. The evaluation must be reviewed periodically, taking into account any changes to our standards or external legislation.
Where the requirements are specific to a site or business risk, Unilever publishes SHE specific standards and separate supporting guidance. For instance, one of our Research and Development centres will have different issues or specific risks compared with an office or Personal Care factory.
SHE specific standards include those for third-party manufacturing (including further standards for new factories), auditing, reporting and verification of management systems, environmental performance reporting, notification and investigation, and reporting of SHE incidents. We have also developed standards for activities such as biomass sourcing and the phasing out of high-impact refrigerants from our operations.
Our Unilever Environmental Care Framework Standard
Based on the requirements of the international ISO 14001 standard for environmental management systems, our Unilever Environmental Care Framework Standard maintains the robustness of ISO 14001, while enabling us to tailor the framework specifically to our operations to drive improvements more effectively. The framework ensures a robust process by incorporating requirements for planning, implementation and operation, checking, corrective action and management review.
Using our own framework allows us to quickly update the requirements of the standard when needed, for example, to reflect emerging best practices or in response to incidents that have occurred.
Internal and external auditing
Regular environmental audits support continuous improvement. All our manufacturing sites are audited regularly (at least every three years) to assess the robustness of their implementation of our Unilever Environmental Care Framework Standard. More than 25% of our sites are audited against this standard every year.
We also provide annual training to ensure all sites and their relevant Safety, Health and Environmental professionals are reminded about the Standard’s requirements and its alignment with ISO 14001.
Audits are conducted either by a third-party auditor or by a trained employee who is independent of the site being audited. The process, similar to that used for ISO 14001 audits, sees auditors gathering evidence to demonstrate compliance against the Standard through the collection of documentation or employee interviews. Where we have ISO 14001 certification, audits are completed annually by a relevant certifying body.
Independent external auditors visit selected manufacturing sites as part of our annual assurance process. They review each site’s processes for collection, collation and validation of environmental and occupational safety data.
Tracking progress
We collect eco-efficiency data from both our manufacturing and non-manufacturing sites using a web-based reporting system. This includes key metrics on environmental performance and qualitative measures on environmental management. Detailed data on utility costs enables us to measure the financial benefits associated with eco-efficiency. Environmental and financial indicators related to eco-efficiency are included in routine management reports.
We’ve been monitoring and reporting the environmental performance of our operations for over 20 years, but we seek to continually improve our processes. For example, we have automated measurement, monitoring and targeting systems at many of our manufacturing sites which enable us to track performance and identify opportunities to improve eco-efficiency using real-time data.
Scope of our data
Our eco-efficiency data covers all our sites globally – in 2022, that was around 250 manufacturing sites. It excludes data from third-party companies that manufacture or pack our products. The annual reporting period for these metrics is 1 October – 30 September.
The annual reporting period for these metrics is 1 October – 30 September.
Our Basis of Preparation 2022 (PDF 755.45 KB) details how we calculate selected eco-efficiency metrics and our sustainability performance data includes a breakdown of our eco-efficiency performance across climate, water and waste.
We report in line with RE100’s best practice on renewable electricity reporting, reporting electricity as 'renewable' when the accompanying Renewable Energy Certificates (RECs), originate in the same market we are operating in. We also include renewable electricity generated at our factories, such as the electricity from our combined heat and power plants (CHPs) and onsite solar installations.
The word ‘organisation’ means all Unilever/Regional/Sub Regional Corporate Head Offices, Operating Company Head Offices, Marketing & Sales Organisations, Sourcing Units, Plantations, Research Development Centres, Warehouses and Distribution Centres. The word ‘organisation’ as used within the Unilever SHE Frameworks Standards does not apply to non-Unilever operations e.g. third-party makers/co-packers. A Unilever Specific SHE Standard which relates to third-party operations has been published separately.