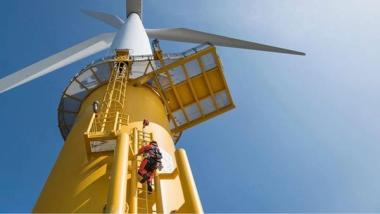
Decarbonising our business
Average read time: 6 minutes
We’ve been taking climate action across our operations for decades and now we’re working to eliminate fossil fuels entirely and switch to renewable energy.
When it comes to climate action, every tonne of carbon counts. That’s why we’ve carefully measured our greenhouse gas footprint to understand where our emissions come from and target our efforts on our journey to decarbonise our business.
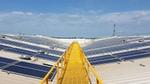
The greenhouse gases we emit from our own factories, offices, research labs, data centres, warehouses and distribution centres, make up only 2% of our total greenhouse gas footprint. Yet the size of our operations means it’s still a significant amount where we have direct control so we’re working to eliminate them entirely.
Our Scope 1 and 2 emissions come from energy and refrigerants used in our own operations, largely in our factories which produce most of our emissions. We’re transforming the way our factories run by investing in new technologies like hydrogen, increasing energy efficiency and switching to renewable energy sources.
We’ve already reduced our global manufacturing carbon footprint by two-thirds since 2008 – but we want to get to zero. We've reduced operational Scope 1 and 2 emissions by 68% since 2015. This puts us on track to achieve our interim milestone of a 70% reduction by 2025. We're taking action in a number of areas to decarbonise our operations.
-68% Reduction in operational Scope 1 and 2 emissions since 2015.
Renewable electricity
Transitioning to renewable electricity is a significant driver of emissions reduction in our operations. As far as possible, this has been delivered through supporting local renewable energy markets – in the form of renewable electricity contracts called Power Purchase Agreements (PPAs) and green electricity tariffs. Where it is not possible to do this, we buy Renewable Energy Certificates (RECs) – openly traded certificates linked to renewable electricity generation – to match our grid power demand.
In January 2020, we reached our target of purchasing 100% renewable grid electricity for our operations through a combination of Purchase Power Agreements (PPAs) and Renewable Energy Certificates (RECs). Since we set this target, we've worked with the RE100 campaign to evolve industry best practice in renewable energy reporting. Since 2021, we have been aligning our renewable electricity reporting with the updated RE100 and CDP guidance in two ways.
First, for renewable electricity certified with RECs, we will only report as '100% renewable' the electricity where the accompanying RECs originate in the same market. The second change is to include non-grid sourced electricity, such as Combined Heat & Power which we use at a limited number of sites (see thermal renewable energy below). Our 2021 Annual Report provides for more detail on these changes.
Taking into account the updated definition and widened scope of our renewable electricity reporting, in 2022, 93% of our total electricity was from renewable sources.
Generating our own renewable electricity
Many of our sites require other forms of energy to power their equipment, so we need to go beyond buying renewable electricity and generate our own renewable power on-site. Our sites are switching from fossil-fuel-based energy systems like coal and gas to clean energy alternatives like wind, solar and biomass. Currently, Unilever facilities in over 18 countries have on-site solar installations. In 2022 we generated 1.4% of our total electricity from on-site renewable sources.
Investing in large-scale renewable electricity
Where we don’t produce our own renewable electricity, we make direct purchase agreements with large-scale solar, wind, hydro and geothermal installations, and small-scale hydropower schemes. For example, around 72% of the electricity we use in Mexico is produced from wind power. In the Philippines, we are now sourcing all our electricity from a geothermal power plant. And in Pakistan, we are pioneering the use of a new in-market certifiable renewable electricity provider to help establish a local supply.
Renewable thermal energy
Our factories need thermal energy for hot air, hot water and steam used in the manufacturing process. We aim to transition heating sources (typically fossil-fuel-burning Combined Heat & Power boilers for hot air, water and steam) to renewable energy alternatives by 2030.
We’re phasing out fossil-fuel-burning boilers and exploring new renewable heating technologies. These include heat pumps, concentrated solar power and lower carbon biogenic-derived sources. Biomass and biogas are important alternatives to fossil-fuel-based gas or coal for heating. We produce our own biogas at some sites, using by-products from our manufacturing processes. For example, Marmite helps power our Burton site in the UK – a by-product from the manufacturing process is converted into biogas for our boilers.
Many of the low-carbon heating options we’re exploring are not yet commercially viable or widely available, so we're supporting innovation and looking for ways to trial them. We believe hydrogen will have an important role to play in the longer term, which is why we’re piloting it at our Port Sunlight site in the UK. See case study above.
Eliminating coal
By early 2020, we had stopped using direct coal on-site for thermal energy, except for three factories acquired in 2020 as part of our acquisition of the Horlicks portfolio in India and other predominantly Asian markets. In 2022, our factories achieved a full year without direct coal use in our operations. We're exploring options to eliminate indirect coal from steam supplied by third parties by 2030. We advocate for the worldwide phase-out of coal through the Powering Past Coal Alliance.
Tackling refrigerant emissions
We’re also retrofitting or replacing our cooling systems with more climate-friendly refrigerants. In many countries where we operate, our policy on refrigerants is significantly more stringent than local regulations, and so we are importing greener refrigerant solutions.
We're phasing out high-impact refrigerants from our operations, starting with the most harmful hydrochlorofluorocarbons (HCFCs). When replacing these, we aim to use the greenest version available for the purpose needed.
Between January 2020 and January 2022, we had replaced HCFCs in larger refrigeration systems (such as process chillers, ventilation systems and cooling systems) at 84 sites, reducing our volume of HCFCs in large systems by approximately 19 tonnes. Replacing these HCFCs reduces the potential for ozone-layer depletion and global warming caused by refrigerant leakage. There are also additional benefits such as improved electrical efficiency of more modern equipment, which often leads to a reduction in overall site electricity consumption, saving money in the process.
Lower carbon offices
While our office greenhouse gas footprint is relatively small, we’re committed to eliminating these emissions too. We’re doing this by: switching to renewable energy; designing new offices to meet strict environmental standards; reducing energy use and using energy-efficient equipment; switching to low-energy LED lighting; supporting teams at each site to take action; and working with our landlords and other partners to find new solutions to reduce emissions. Since 2010, we’ve more than halved CO2 emissions from energy used in our offices.
Reducing food waste
Our first priority is to reduce the amount of food waste we generate in the first place. This also helps reduce our GHG emissions. We're exploring solutions with our engineering teams to halve food waste in our operations by 2025 such as anaerobic digestion, using the biogas generated on-site, composting and using the waste as fertiliser. Read more about how we’re tackling food waste.