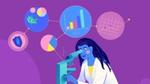
Sustainability Reporting Centre
Our key policies, waste data and details of our material issues can be found in our Sustainability Reporting Centre.
Unilever Global Change location
Average read time: 5 minutes
We’ve spent many years reducing waste and recycling in our operations and we continue to look for innovative ways to eliminate and extract value from our waste streams.
More than two-thirds of our manufacturing waste is from biological sources (such as sludge from wastewater and inedible food waste). Where this waste is unavoidable, we look to extract value from these streams by finding reuse opportunities (such as animal feed), or recycling and recovering into new products (such as biogas capture via anaerobic digestion or composting back to agriculture use). See Tackling food waste for more on how we’re recovering food waste in our factories.
Our key policies, waste data and details of our material issues can be found in our Sustainability Reporting Centre.
Other forms of non-hazardous waste streams generated include raw materials and product materials (plastics, cardboard, paper and packaging waste). Technically we look to improve our recycling and recovery rates of these materials – which accounted for 96% of total waste in 2022. Much of this process occurs on site or, in partnership with recyclers.
-96% Reduction in waste disposal per tonne of production since 2008
We continue to maintain our standard to send zero non-hazardous waste to landfill from our factories.* An accomplishment we have achieved since 2015 and an industry first at our scale.
To achieve this, each factory undertook a detailed mapping of mixed waste streams and considered every material consumed. Our dedicated collection and storage points make waste segregation easier at sites. We also trained employees involved in waste management to come up with detailed action plans for reuse, recycling or recovery. Where we find approaches that work, we transfer them to other sites around the world.
We’ve since extended our zero waste mindset beyond our factories to other parts of the business – including offices, distribution centres and warehouses.
Our zero waste mindset means we look at waste materials as a resource. Where we’ve not been able to find ways to refuse or reduce waste, we look for routes to reuse or recycle it. And if these solutions aren’t available, we recover energy from the waste. By finding the best routes for material flows, we strive to strengthen our circular economy approach – improving factory operations and reducing our environmental impact.
Our waste reduction journey starts with refuse – that is, avoiding waste being generated in the first place. Eliminating or reducing waste at source is the best way of cutting our environmental impact and creates the most opportunities for savings. For instance, at many sites, we require suppliers to use returnable pallets and containers, thereby limiting the amount of waste that we need to manage. And our Nashik factory in India is now using reusable containers for its chocolate supply, improving its relationship with the supplier and reducing the amount of plastic waste generated via reverse logistics.
We want to be as efficient as possible at converting raw materials into products and reducing the amount of waste generated. We don’t stop here. We focus our efforts on all material coming through the factories. For example, at our Casalpusterlengo Home Care factory in Italy, forklift trucks are now using lithium batteries, which not only consume 25% less energy but also last three to four times longer than lead ones.
Several of our sites are working with their suppliers to reduce the packaging that raw materials are delivered in. Our Nashik factory in India, for instance, receives their jam pulp in drums that can be washed and reused over and over again reducing metal waste generation by over 100 tonnes a year.
Our aim is to get the most possible value from materials, therefore, we look for ways to reuse them ourselves or make them available for others. In recent years, we’ve increased our reuse rate by 20%, keeping materials in the circular economy for longer. When others reuse the materials we no longer need, we don’t count this as a waste because it helps reduce the consumption of natural resources in other industries.
For example, in our Cuernavaca factory in Mexico, we receive raw materials and packaging in cardboard boxes. We found that these boxes can be reused by other industries, such as for transporting snacks around the country. In our UK factories, almost all our cardboard boxes are returned and reused for new packing material deliveries.
We are also working on a project in the Philippines which uses earthworms to transform low grade food waste into animal feed protein.
The majority of our waste is recycled, sometimes in innovative ways. For instance, our Pouso Alegre factory in Brazil composts organic waste and uses this to fertilise fruit gardens that grow food for the staff canteen. At our Carrascal site in Chile, we have created a garden with furniture made from pallets, and plant pots made from drums. For most sites, recycling means segregating waste into paper, plastics, metal and glass, and we can often sell this to recycling companies for them to make into new products.
Some of our sites have extended their waste programmes to ensure that their employees also have a way to recycle the waste they generate at home. Our Pouso Alegre site in Brazil implemented an ‘eco-point’ recycling area for employees to use at the entrance to the factory. And our St Petersburg factory in Russia has a similar collection point that allows employees to dispose of hazardous waste like batteries and mercury thermometers in a safe way.
Where we have not yet found routes for recycling, we recover waste materials and use them to generate energy. At many of our factories around the world, we do this through our global partnership with the cement manufacturer LafargeHolcim and its waste management service provider Geocycle. Our waste materials are pre-treated and used as alternative fuel and raw material in their cement kilns. Even the ash is used – it’s fully incorporated into the cement clinker, so it doesn't leave any residues.
In our facilities at Heppenheim, Burton and St Albans, we continue to recover value from unavoidable waste streams by extracting biogas from anaerobic digestion to fuel some of our thermal heating demand – an innovative solution to aid our decarbonisation programme.
We aim to maintain our achievement of zero non-hazardous waste to landfill (ZNHWTL) across our manufacturing sites worldwide. However, incidents can occur where small amounts of non-hazardous waste are sent to landfill in error or because of operational changes e.g. Covid-19, acquisitions or supplier issues. We consider ZNHWTL is maintained when less than 0.5% of non-hazardous waste is disposed to landfill in the 12-month period.